Společnost Yaskawa nabízí portfolio produktů, díky kterým je předním výrobcem v oblasti měničů střídavého proudu, servopohonů, řídicí technologie a robotiky.
Roboty MOTOMAN a paletizační systémy EGS automatizují obráběcí stroj Fintes v Hittisau
Společnost Fintes GmbH z Hittisau/Vorarlbergu hledala spolehlivý, flexibilní a odolný systém pro automatické podávání obráběcího centra s nejlepším možným poměrem ceny a výkonu. Současně měl být systém co nejjednodušší na obsluhu. Autonomie měla být také co největší z důvodu ekonomické efektivity. Nejednalo se o první robotický automatizační systém, který společnost EGS Automation dodala společnosti Fintes; v závodě v Hittisau jsou v provozu již dva systémy, první z nich od roku 2014.
- Průmyslové odvětví
- Automobilový průmysl
- Aplikace
- Paletizace
- Manipulace s materiály
- Kient/ zákazník
- EGS Automatisierungstechnik
- produkty
- GP25 - GP řada
Automatizační systém vyvinula a realizovala na klíč společnost EGS Automation GmbH z Donaueschingenu v okrese Schwarzwald-Baar. Tato společnost působí v oblasti průmyslové automatizační techniky od roku 1996 a průmyslové roboty používá od roku 1999. V roce 2014 si společnost Fintes nechala poprvé nainstalovat systém od společnosti EGS pro automatizaci montážního procesu zahrnujícího servo lis. V roce 2019 následoval automatický podavač pro obráběcí centrum. Pro třetí systém byl vybrán také SUMO Multiplex od společnosti EGS, paletizační systém ze standardní řady EGS, který pracuje na principu paternosteru. Ve všech třech systémech manipuluje s obrobky robot Motoman od společnosti Yaskawa.
Paletovací systém SUMO (standardizovaný, univerzální, s minimálními nároky na prostor, optimalizovaný)
SUMO Multiplex je 12násobný paletizační systém určený pro palety o rozměrech 600 x 400 mm. Používají se základní palety EGS, které jsou pomocí vložek individuálně přizpůsobeny obrobkům. Jednotlivé palety s hotovými díly lze kdykoli vyjmout nebo vložit nové palety s nedokončenými díly - to nemá vliv na proces automatizace.
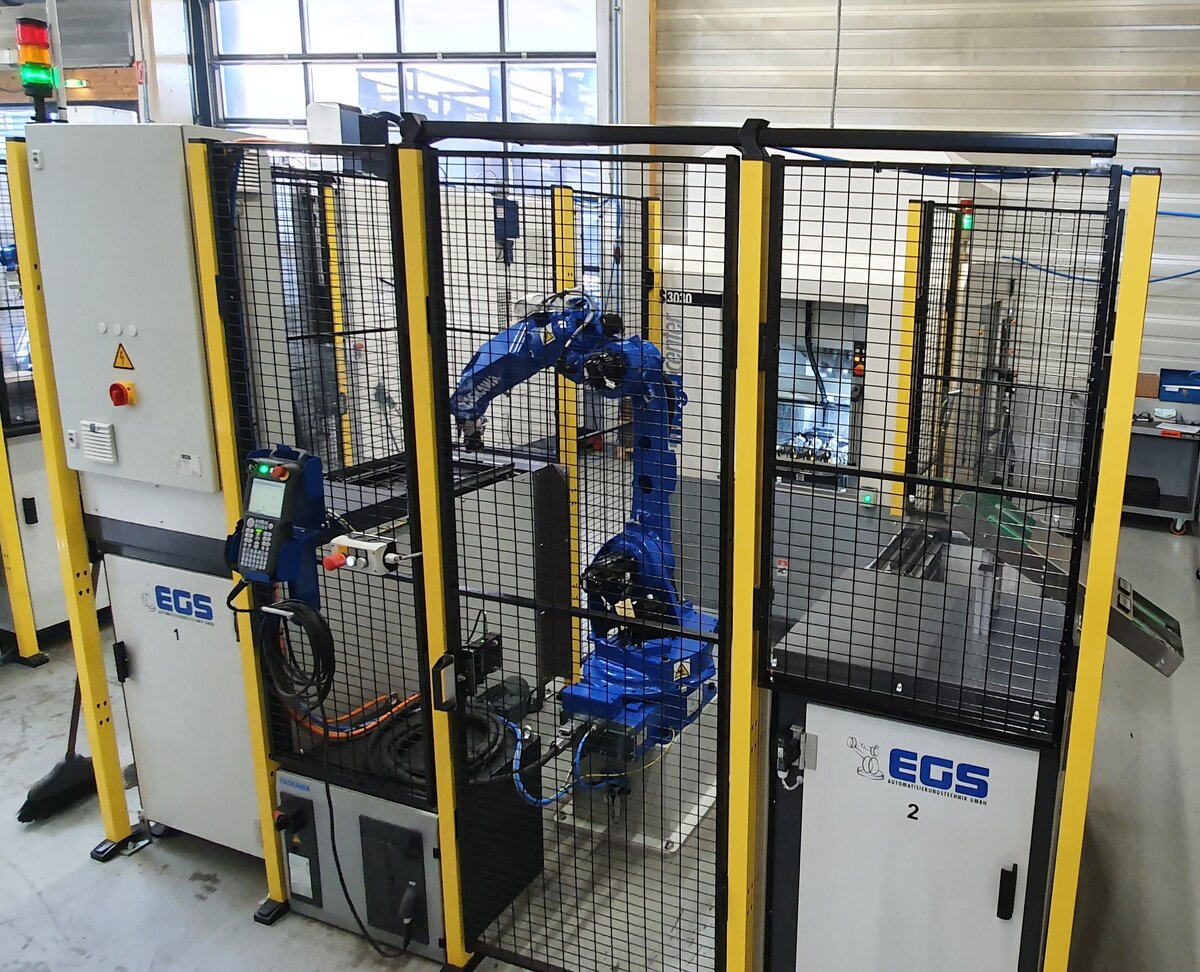
Assembly with high-precision workpieces
The SUMO Multiplex has the task of automatically loading and unloading a Müga S3030 machining centre with workpieces. These are precise engine components - more precisely, pump housings for luxury class vehicles, which are triple machined on the machine. Thanks to a shuttle table, the Müga S3030 makes it possible to change parts while simultaneously machining three parts on the outside of the table during machining.
The robot is a Motoman GP25 from Yaskawa with 25 kg payload and a reach of more than 1.7 m. The equipment with a workpiece-specific double gripping tool enables cycle-time-optimised parts handling. This is necessary because the machining time for three parts is 60 seconds and, in addition to the part change, each clamping point must be cleared of chips before the next blank is inserted; this is done by the gripping tool equipped with a blow-off device, which removes the chips by means of compressed air.
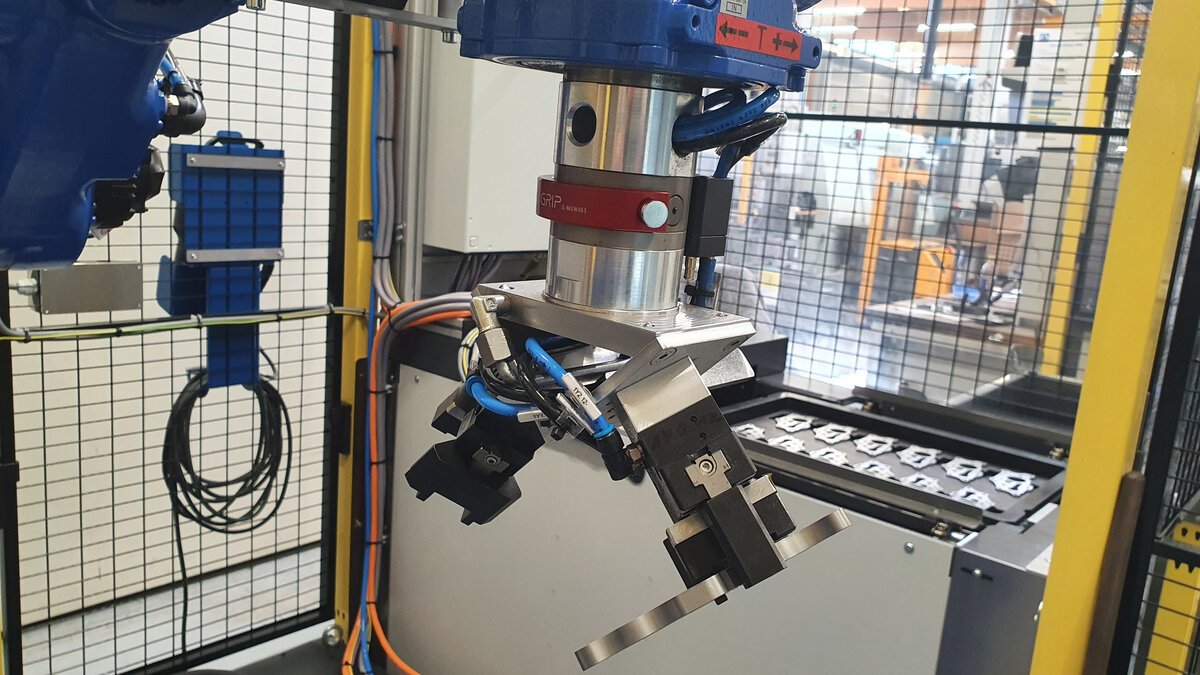
Efficiency, economy and speed
12 parts fit in one pallet, which, with the processing time of 60 seconds for three parts, results in an autonomy of approx. 50 minutes for a palletising system. That was not sufficient for Fintes, so they decided on a system with two palletisers, both operated by a robot. This allows the autonomy of the entire system to be doubled to just under 2 hours. In addition, the system offers a QA part output, which outputs a test part on request. Furthermore, there is a nio-part output; if the machine reports a machining error after machining, the robot does not put these three parts into the finished part pallet, but outputs them via this workpiece chute. EGS coordinated directly with the machine manufacturer with regard to the design of the interface. As an experienced automation specialist, we are used to adapting to the given machine conditions.
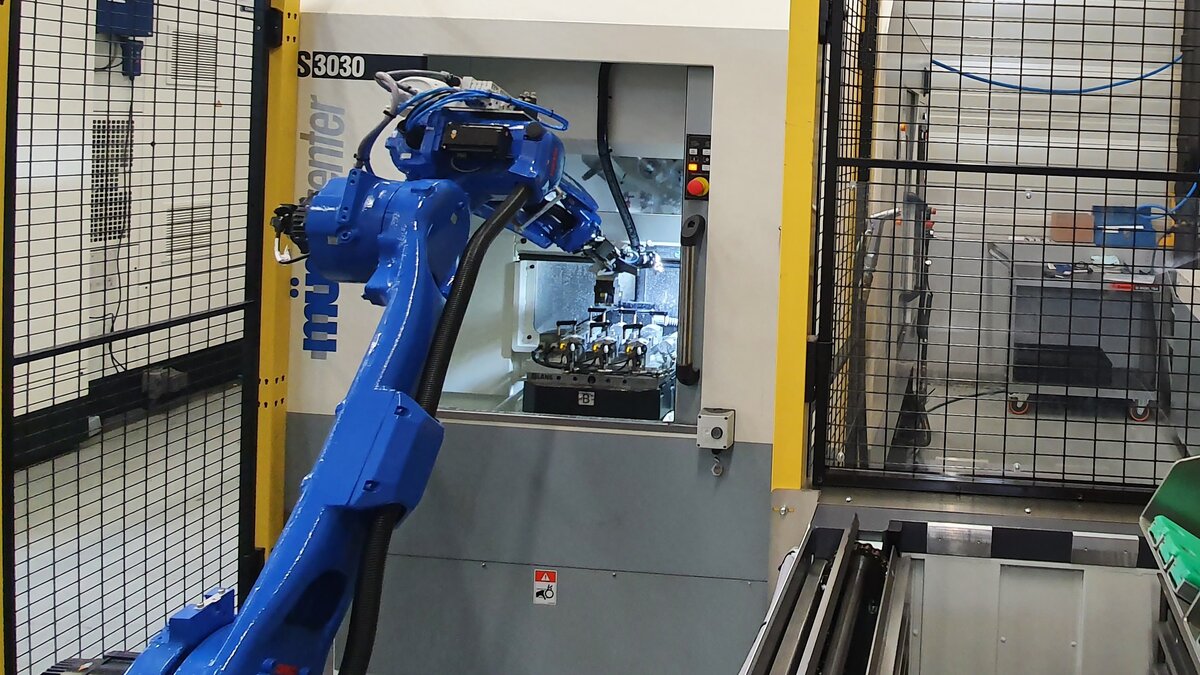
Placing the robot optimally
Thanks to its reach, the robot allows positioning at an optimum distance from the machine, so that access for set-up or manual operation of approach parts or small batches is easily possible through the large safety gate of the safety fence. The floor scanner version without a protective fence was out of the question for Fintes. "This option only appears to pay off. This is because the area in front of the machine looks as if it is free, but it can’t be used because the robot would otherwise only run at reduced speed or even stop because of the required safety distances. This means that in the evening, you have produced less and are at a loss why this is so,” says Stefan Heidegger, assistant manager at Fintes explaining his decision.
Designed for the future
In order to be able to work flexibly in the future, the robot is equipped with a gripper changing system. If you want to produce other parts on the machine, a second double gripping tool can be mounted in just a few steps. The gripper can thus be changed in a few minutes without tools.
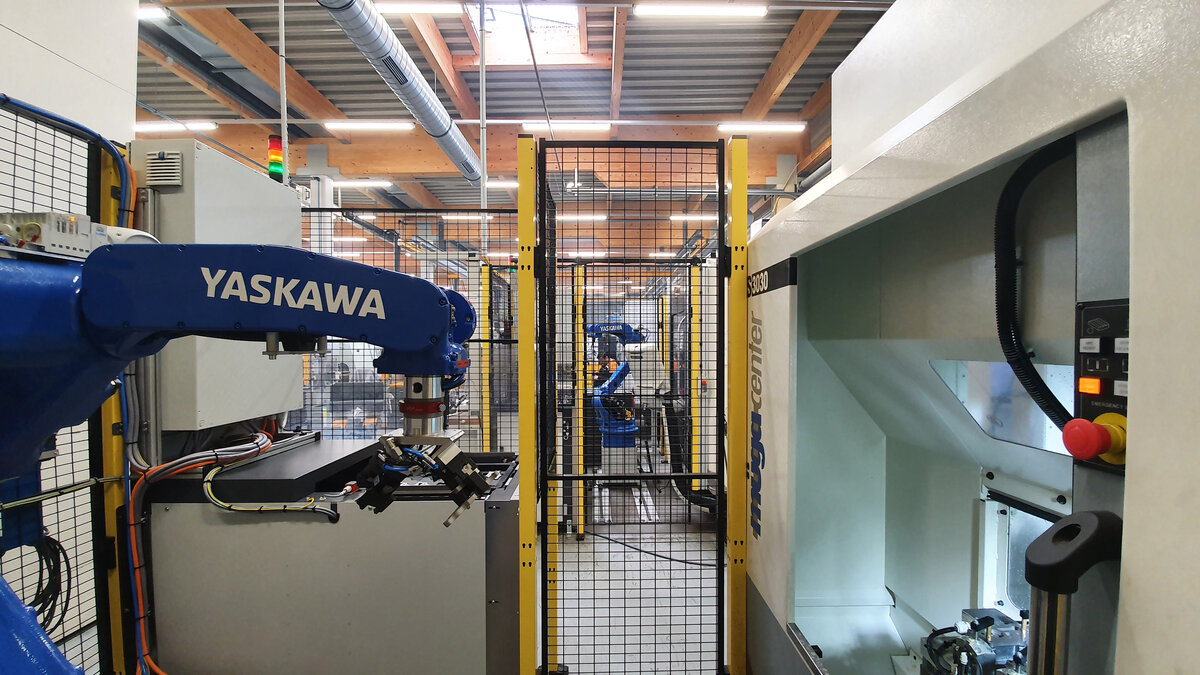
Proven technology for Fintes
The third system now features the third Yaskawa robot in use at Fintes. This robot, designed and optimised for machine tool automation and the corresponding environmental conditions, is easy to control using the robot programming handset. The robot controller, which is responsible for the entire automation, is in charge of both palletising systems, calls up probe and sensor data and forms the interface to the processing machine based on teh Profinet interface. Operation is carried out using a touch screen on the programming pendant. Other important features are the start-up and empty routines until all positions in the circulation are filled with parts or emptied, as well as an automatic safety speed for the first cycles after restart. Fintes is fully satisfied with the three robot systems from EGS. "We were convinced by the quality of the workmanship and the reliability in daily operation of the EGS systems from the very first installation.
The SUMO Multiplex is a simple and robust palletising system. The ability to remove or add individual pallets at any time gives us maximum flexibility," concludes Stefan Heidegger.
Fintes was founded in 1996. It manufactures turned parts for the automotive industry as well as aluminium parts in small series. Thanks to the high quality and many satisfied customers, FINTES is rapidly becoming a sought-after company with an excellent reputation. As early as 1997, FINTES founded the company FINTES s.r.o. in Pribraz in southern Bohemia as a 100% subsidiary. In 2000 and 2003, further production halls were built in the Czech Republic due to the high demand. Only three years later, a new company building was erected at the headquarters in Hittisau, which houses not only production but also development and administration. In 2021, Fintes employs a total of almost 130 people at both locations with more to come. The product range currently includes turned and milled parts made of stainless steel and other materials in small and large batch sizes. If required, Fintes also supports customers during the development phase. The portfolio also includes the assembly of complete sub-assemblies according to customer requirements.
Pictures: Fintes GmbH
Author and Contact:
EGS Automation GmbH
Heiko Röhrig, Leiter Vertrieb & Marketing
Fon +49 771 898 606 27
Contact readers’ enquiries Yaskawa:
Tel. +49-8166-90-0
Fax +49-8166-90-103